Subject matter expert (SME) in FDA Compliance
FDA Regulatory Consulting
Welcome to RAQA, an FDA Regulatory Consulting firm, also known as your regulatory resource by former FDA scientists, reviewers, investigators, compliance officers, and managers. We are subject matter experts (SMEs) in the regulatory and quality field, specializing in detecting non-conformities, assessing, analysing, and preventing adverse effects of medical devices, in vitro diagnostics, biologics, and pharmaceutical drugs.
When you choose our consultants who once served as FDA investigators, you’re getting far more than regulatory advice. You’re gaining direct insight from professionals who understand how the agency thinks, operates, and enforces laws. That perspective cannot be taught—it’s earned through years of fieldwork and compliance evaluation.

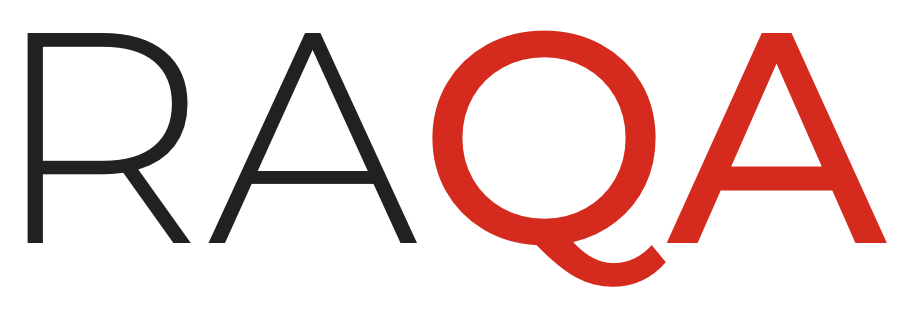
We’ve been there and done that!
Extensive experience with FDA compliance, including the issuance of numerous Warning Letters, seizures, injections, and the review of responses to FDA-483.
FINDING THE RIGHT FDA CONSULTING FIRM
Finding the right consulting firm for your industry is more challenging than you might think. There are numerous corporate and independent consulting companies available, each promising excellent results. However, as drug, biologics, or medical device manufacturers, it’s ultimately your responsibility, regardless of the outcome. Therefore, finding a proper regulatory consulting firm for your needs is critical.
At RAQA, we have both FDA and industry experience. We understand and have expertise on both sides. We can “think” like the FDA, from mock FDA inspections to regulatory submissions.
OUR FDA CONSULTING SERVICES INCLUDE:
-
- Mock FDA Inspections – Medical Device QSR, Drug CGMP, OTC, Cosmetic, GLP, GCP, HACCP, ISO, and Animal Drug & Feeds.
- Present during an FDA Inspection
- Supplier’s Vendor Quality CGMP Audits
- Recalls, removals, and field corrections
- Regulatory submissions (Premarket Notification (PMN) 510(k), PMA, NDA, ANDA)
- Submission of a food additive petition for approval
- Review Warning Letters (WL) and FDA-483, Inspectional Observations, responses
- CAPA (Corrective and Preventive Actions)
- CGMP, ISO, QSR Training
- Registrations and Listing
- Review standard operating procedures (SOPs) and quality system manual
- Label & labelling reviews, including websites and dietary supplements
- Quality Management System (QMS)
- Validations: computer system, water for injection (WFI), purified water, sterilisation, cleanroom, aseptic filling, formulation, process & automation, software, and packaging.
Furthermore, finding quality staff with FDA experience is particularly challenging. Designate us for all your FDA-related needs. The location of your manufacturing facility is not a concern since we are conveniently located in Asia, US, and Europe. For short-term mock FDA inspections or long-term FDA consulting, contact us today.
FDA CONSULTING BY EX-FDA
Whether you have recently started a company or have hired new quality staff, compliance with the FDA laws and regulations comes first. If you have doubts and want to examine your quality manual in greater depth, RAQA is here. We can also conduct mock FDA inspections to review and align your compliance with the CGMP or ISO.
No matter what your issues are, we can help you in time.
However, please don’t wait until the FDA knocks on your door. Instead, allow our former FDA investigators to look closely at your CGMP and make appropriate corrections.
Human & Animal Health Industries
Quality should be your top priority for every manufacturer that handles products related to human and animal health. Because the FDA never inspected your facility, it doesn’t mean you don’t have to comply with the United States Federal Food, Drug, and Cosmetic Act. Even though the FDA has not inspected your company for the past 20 years, it doesn’t mean you are not under their radar. Your firm may be the lower priority in their work schedule, but the FDA monitors and comes when they deem necessary. Therefore, being ready all the time is your responsibility.
Unmatched Expertise from Inside the FDA
FDA Consulting from former investigators offers a level of precision and depth that is hard to replicate externally. They’ve walked into countless facilities, reviewed procedures, and issued observations based on firsthand interpretation of the law. Notably, this allows us to anticipate regulatory trends, enforcement focus areas, and potential red flags before they surface.
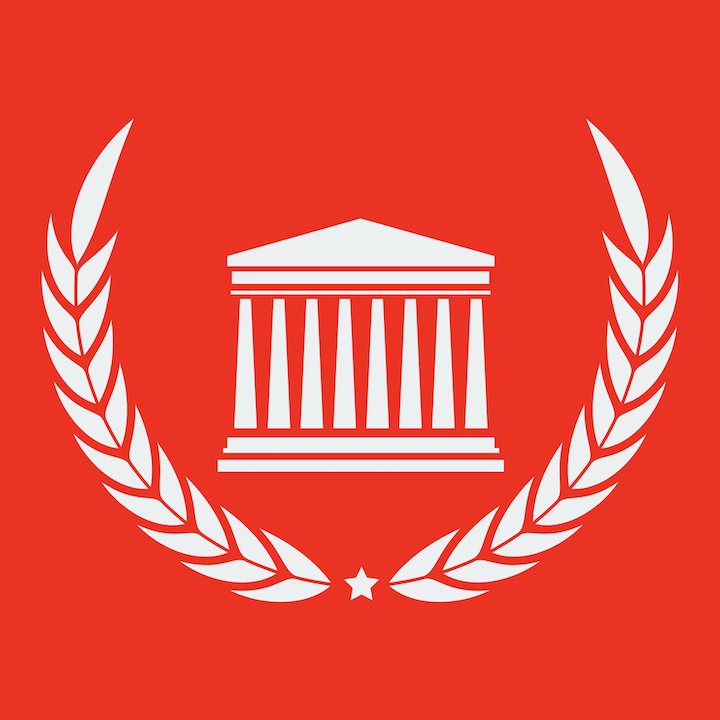
Today is the time, not tomorrow.
Please note that because you are certified in ISO 13485, it doesn’t automatically comply with 21 CFR 820. Let us come in and evaluate your compliance with the new regulation.
“Quality Culture” FDA Consulting
As a medical products manufacturer, FDA compliance should not be your rationale for establishing a quality system. Simultaneously, you can ignore the quality because you don’t export products to the USA. Quality should be “built-in” as long as you handle medical products regardless of the regulations and laws. As such, we call this the “quality culture.” In other words, you should adopt a quality system for your company, regardless of compliance, laws, and regulations issues. Moreover, it involves everyone, departments, and the process of handling medical products.
What are the FDA laws?
The U.S. FDA regulates medical products through various laws and regulations. The main statutory laws are the Act and 21 CFR. Additionally, the FDA publishes guidelines documents that reflect their interpretations. At RAQA, our consultants are trained and experienced in the application of these laws and regulations.
What Is The Current Good Manufacturing Practice (CGMP)?
The CGMP is outlined in the 21 CFR, Code of Federal Regulations, Title 21. Relevant manufacturers must adopt customised good manufacturing practices for their unique manufacturing processes. Therefore, duplicating other manufacturers’ CGMP may not be adequate. We have been there in an official capacity. As such, we understand better what officials expect when they come to your manufacturing plant. In addition, we pass our experiences and knowledge on to your quality staff.
You Can Better Prepare For An Upcoming Audit By Choosing FDA Consulting.
However, it’s prudent to be proactive, so you’ll have plenty of time to correct any deficiencies identified during the mock FDA inspection. Waiting until you receive notification of an upcoming inspection from the FDA may not have ample time to identify and fill the gaps in the quality system.
The Purpose Of Our FDA Consulting
- First, your quality system must be flawless to succeed and lead in today’s aggressive and competitive market.
- Our experienced ex-FDA investigators are in the most qualified position to consult on FDA matters.
- It’s the most beneficial, inexpensive way to go through an FDA inspection.
- A strategic way to train your staff is to be psychologically prepared for FDA inspections.
- Finally, avoid non-compliance history; someone can use them against your company.
Medical Device And In-Vitro Diagnostic (IVD) Manufacturers
The Code of Federal Regulations CFR, Part 21 Section 820, also known as Quality System Regulation (QSR). The inspection method is the Quality System Inspection Technique (QSIT). US FDA adopted QSR in 1997 to help medical device manufacturers comply with 21 CFR 820.
By enacting The Federal Food, Drug, and Cosmetic Act, Congress gives the FDA authority to monitor the safety of food, drugs, medical devices, and cosmetics. For some, this Act is a challenging and complex US law. Nonetheless, it governs your medical products. That’s why you will need our FDA consulting services.
What’s New QMSR?
It is the revised part 820 of the Quality System Regulation (QSR). On August 7, 2024, the FDA published the Quality Management System Regulation (QMSR): Final Rule Amending the Quality System Regulation, which is in effect on February 2, 2026.
It aligns closely with the international consensus standard for Quality Management Systems of medical devices recognised by many regulatory authorities worldwide. However, the FDA has yet to develop a new inspection process as of writing this section. At RAQA FDA Consulting, we understand how you can prepare to meet the new regulations that affect you.
Please don’t wait until you get a notification of an FDA inspection before consulting with us.
Not all former FDA employees possess the expertise you need.
Hiring former FDA officials with extensive FDA backgrounds for your organisation may be out of reach. Just because of ex-FDAers doesn’t mean they meet the job qualifications. This is where our FDA Consulting comes in convenient. We have an expansive background in the FDA to consult with every question, be it the laboratory, regulatory, CAPA, compliance, inspection, quality management, regulatory submissions, corrective actions, recall, or validations.
In addition, we can comprehensively examine and align your quality system with FDA regulations and other requirements. In fact, our mock inspection is designed exclusively to examine and test your company’s quality policy to reveal any gaps or problems before an FDA inspection.
We Are Your CAPA Subject Matter Experts (SME)
Proactive CAPA Systems Prevent Escalation
Corrective and Preventive Action (CAPA) systems are a cornerstone of FDA-regulated quality systems. Whether under 21 CFR Part 820 for medical devices, 21 CFR Part 211 for pharmaceuticals, or ISO 13485 for international firms, CAPA compliance is essential for identifying, investigating, and resolving product and process nonconformities. CAPA failures are one of the most frequent causes of FDA 483 observations and Warning Letters. Companies often struggle not with writing procedures, but with consistently implementing them, ensuring traceability, and conducting root cause analysis.
FDA Regulatory Consulting offers specialized expertise in evaluating your current CAPA structure, identifying system weaknesses, and developing a compliant and efficient process tailored to your specific operation. Also, many organizations initiate CAPAs too late or treat every deviation as equally urgent. This clogs the system and hides truly critical issues from leadership visibility.
Root Cause Is More Than Asking “Why?”
Effective CAPA begins with a robust root cause investigation. Simple tools like “5 Whys” are often insufficient for complex systemic issues. Root cause must go beyond symptoms to underlying contributing factors, whether procedural, training-related, or cultural. Moreover, regulatory bodies expect statistically rationale plans for chosen root causes and justification for rejected materials. This transparency strengthens your audit readiness and internal quality culture.
Additionally, many firms rush from investigation to action without verifying effectiveness. The FDA now closely reviews how companies define and measure CAPA effectiveness, including long-term monitoring. Furthermore, leadership must be involved in CAPA review. Management oversight ensures accountability and resource alignment.
Not All ISO Certifications Are Equal
Although the QMSR is built around ISO 13485:2016, it is enforced through FDA inspections, not third-party audits. This changes how manufacturers prepare for compliance. The FDA focuses more heavily on post-market surveillance, enforcement actions, and specific process validations.
Beyond the Protocol
Process Validation is not a one-time event; it is an ongoing process. It’s a lifecycle approach to ensuring consistent product quality across manufacturing runs.
Real-World Application, Not Just Theory
Unlike textbook consultants, our experts bring actionable knowledge rooted in real-world investigations. We know precisely what the FDA looks for during inspections, because we used to conduct them. Therefore, our audits are structured in a manner similar to actual FDA visits. FDA Consulting at this level prepares your team in the most authentic way possible, from documentation to behavior during interviews.
Additionally, our consultants understand the pressure companies face when receiving a Form 483 or Warning Letter. We’ve issued them before and now help businesses respond strategically. Also, mock inspections led by former investigators are often more rigorous than official visits, providing a significant compliance advantage.
Customized Support Across Product Types
Every product type—device, drug, biologic—requires a different compliance strategy. Our consultants tailor each solution to match both your product and your company’s risk profile. As a result, the advice is not generic. FDA Consulting from former regulators adapts with your evolving business and compliance needs.
We offer in-depth insight into inspection readiness, design controls, validation strategies, and management controls. Moreover, we assist in crafting responses that align with current regulatory expectations, rather than relying on outdated templates. However, the real strength lies in their ability to educate internal teams and foster a long-term culture of quality.
FDA Consulting, Confidence Rooted in Experience
Former FDA investigators offer more than technical skill. We provide confidence grounded in lived experience. We’ve seen companies succeed and fail, and we know what separates the two. Thus, our guidance is not based on opinion but on patterns proven over time. Our consulting from these experts often prevents costly mistakes before they occur, helping you stay one step ahead.
Furthermore, we bridge the communication gap between regulatory expectations and business execution. This alignment saves both time and money. Even when the stakes are high—such as during FDA inspections, recalls, or pre-approval inspections—former FDA professionals know how to navigate with authority and expertise.
Process Validation
Whether you’re validating a sterile fill line, lyophilization cycle, tablet press, or a software-controlled system, the FDA requires documented evidence that the process consistently produces a product that meets specifications.
Regulations under 21 CFR Parts 820, 210, and 211 emphasize validation as a key quality element. Yet many companies struggle to design protocols that capture true process capability. FDA Consulting supports manufacturers through all three stages of process validation: Installation Qualification (IQ), Operational Qualification (OQ), and Performance Qualification (PQ).
Also, validation begins before protocol writing. Risk assessments, user requirements, and equipment specs must be aligned. Missing these foundations leads to incomplete protocols or failed lots. Furthermore, validation must be product- and process-specific. Copy-paste templates rarely meet FDA expectations and often trigger 483 observations during inspections.
Data Integrity and Protocol Execution
Executing validation is not just about running batches. It’s about recording, reviewing, and interpreting data under strict controls. Poor documentation or inconsistent execution undermines the entire validation effort. Therefore, companies must ensure data integrity is maintained throughout testing. This includes accurate recording, legibility, traceability, and contemporaneous entries.
FDA Consulting helps establish validation master plans, define acceptance criteria, and support teams during execution to ensure inspection-ready data sets. Also, many facilities fail to link validation back to change control systems. Equipment upgrades, software patches, or utility changes must trigger impact assessments and, if needed, revalidation.
Moreover, training records and SOP references must be integrated into validation packages. The FDA expects operators executing protocols to be qualified and use current, approved instructions. Additionally, validation summary reports must include statistical justifications, rationale for batch sizes, and disposition status. This proves the process is both robust and compliant.
Challenges in Global and Multi-Product Environments
Multi-product facilities and global manufacturers face more complex validation challenges. Shared equipment, campaign manufacturing, and different regulatory standards add to the burden. Also, multi-product environments must include cleaning validation, cross-contamination risk assessments, and bracketing strategies. These are often overlooked until FDA questions arise.
Furthermore, small changes in process parameters may require justification through a documented understanding of the process. Temperature ranges, fill volumes, and machine speeds all impact validation conclusions. Moreover, lifecycle validation includes ongoing monitoring through control charts, trending reports, and deviation tracking. Validation doesn’t end after PQ; it evolves with the process. Thus, having a validation team that understands both technical and regulatory requirements helps avoid costly rework or post-market complaints.
Supporting Your Validation Readiness
Validation readiness is more than a compliance task; it’s a business asset. Properly validated processes reduce batch failures, support regulatory submissions, and improve customer confidence. FDA Consulting assists with gap assessments, protocol development, onsite execution support, and inspection preparation. Consultants help teams understand not just what to do, but why it matters. For example, they can identify if a vendor qualification package is missing or if critical utilities, such as HVAC, WFI, or nitrogen, require performance data to be included.
Additionally, FDA consultants guide teams through mock audits, focusing on process validation and ensuring compliance with regulatory requirements. This provides validation that the packages are both audit-ready and technically sound. In addition, validation metrics must be part of the management review. Batch rejection rates, rework incidents, and trending deviations all reflect the process. Therefore, process validation should be viewed as a continuous system, rather than an isolated document set.
Compare New QMSR and ISO 13485
Harmonizing FDA and International Quality Systems
The FDA’s finalization of the Quality Management System Regulation (QMSR) in 2024 represents a strategic alignment with the ISO 13485:2016 standard. For medical device manufacturers, this harmonization simplifies global compliance, provided it is implemented thoughtfully. QMSR replaces QSR, adopting ISO 13485 as its baseline while maintaining certain FDA-specific expectations. FDA Consulting is essential in this phase, as FDA consultants decode both frameworks and highlight key areas that require adjustment to meet domestic and international expectations.
While both standards emphasize risk management, documentation, and process control, QMSR still mandates compliance with federal regulations. For instance, CAPA and complaint handling follow distinct pathways under the FDA. Internal audits, training systems, and supplier controls must now meet the spirit of ISO while satisfying specific FDA expectations. Failure to address these nuances could result in inspection findings.
Structural and Terminology Differences
ISO 13485 and QMSR share a common skeleton, but their internal vocabulary and structure differ in key ways. FDA Consulting supports document harmonization efforts, ensuring that global and domestic requirements are integrated into a single, validated quality management system. Consequently, a company’s inspection readiness must reflect both sets of expectations, especially if pursuing both FDA and international market access.
Risk Management and Process Validation
Although ISO 13485 introduced risk management into design and manufacturing processes, QMSR reinforces this integration more explicitly. Under QMSR, risk must be addressed not just in design files but also in complaints, purchasing, and production. FDA Consulting provides the tools to map risk processes across all operational layers, ensuring they are not siloed or inconsistent. Moreover, QMSR includes a deeper emphasis on process validation, particularly for software, sterilization, and automated systems. These expectations go beyond the general guidelines in ISO 13485.
Furthermore, FDA inspectors will expect traceability from design through post-market activities. Validation files must include clear rationales, acceptance criteria, and evidence of protocol execution. Also, medical device manufacturers must track process outputs through CAPA, trending reports, and continuous improvement metrics that align with both standards. Thus, organizations must adopt a holistic view of validation and risk, not one driven solely by product development.
FDA Consulting: Global Integration and Dual Audit Readiness
With many companies operating in both U.S. and international markets, aligning QMSR and ISO 13485 allows for a unified quality management system. This consolidation reduces documentation burden and audit fatigue. As such, our expertise is especially valuable in developing a dual-compliant system that passes both FDA inspection and ISO audits with minimal friction. For example, firms participating in the Medical Device Single Audit Program (MDSAP) benefit from the early integration of ISO principles with QMSR documentation. However, participation in MDSAP does not exempt firms from QMSR enforcement.
Additionally, ISO 13485 allows some flexibility in documentation format, whereas QMSR imposes more rigid expectations on traceability and formal recordkeeping. Therefore, companies must be cautious not to assume that ISO certification alone fulfills the FDA’s expectations. FDA auditors may pursue issues not addressed during ISO audits. Ultimately, dual readiness is not just about meeting two standards. It’s about maintaining a quality culture that withstands any audit.
QMSR and ISO 13485
Understanding the QMSR Transition
In early 2024, the FDA finalized its overhaul of 21 CFR Part 820 by replacing the Quality System Regulation (QSR) with the Quality Management System Regulation (QMSR). This shift aligns the FDA’s framework more closely with ISO 13485:2016, the international standard for medical device quality management. For medical device manufacturers, this change represents both a challenge and an opportunity. The QMSR streamlines compliance with global markets but requires companies to reassess their procedures, training, and documentation practices.
FDA Consulting becomes critical during this transition. We can help map existing quality systems against ISO 13485 and identify gaps requiring remediation. Although the intent is harmonization, compliance isn’t automatic. The FDA will still inspect according to QMSR requirements. As such, your documentation, CAPA, design controls, and management responsibilities must reflect the updated rule. Internal audits and training programs may also be updated. Some manufacturers may need to revise their supplier agreements and validation protocols to meet the new expectations.
How Does the New QMSR Affect Medical Device Manufacturers?
Key Shifts in Quality Management Expectations
One of the biggest impacts of the QMSR is the integration of risk management throughout the product lifecycle. While QSR referenced risk-based thinking, ISO 13485, and now the QMSR, requires formal risk documentation and ongoing assessment. Therefore, manufacturers must demonstrate how risk controls are implemented and monitored, not just how they are initially identified. This includes updates to procedures for nonconformance, design validation, and post-market surveillance.
FDA Consulting offers a structured methodology for building risk-based systems. Without this support, many companies struggle to meet the nuanced expectations now embedded in the regulation. Also, management review must include metrics on quality objectives, audit results, complaint trends, and supplier performance. Documentation should reflect this focus on continuous improvement. Additionally, companies will need to shift from prescriptive FDA language to ISO-based terminology. SOPs, forms, and training materials must be revised accordingly.
Supplier Controls and Documentation Upgrades
Another area where QMSR raises the bar is supplier management. The FDA now expects medical device firms to implement stronger controls around supplier qualification, monitoring, and re-evaluation. Thus, your purchasing controls must document how suppliers are selected, what performance metrics are monitored, and what happens when a supplier underperforms. FDA Consulting is instrumental in redesigning supplier oversight systems that meet these expectations while remaining operationally efficient.
Moreover, manufacturers may be required to requalify existing suppliers under updated criteria. These activities must be documented and tied to the risk level. Training documentation also receives heightened attention. It’s not enough to show that training occurred. The firms must demonstrate that employees understood and retained the material. Furthermore, internal audit programs must expand to reflect new documentation requirements and risk-based thinking. Sampling approaches, audit scope, and frequency must be defensible and strategic.
Strategic Alignment with Global Compliance & FDA Consulting
With the implementation of the QMSR, the FDA has signaled a long-term intention to harmonize with global regulators. This benefits manufacturers aiming for EU MDR or MDSAP certification. We assist with this alignment by helping organizations build a unified QMS that satisfies multiple authorities simultaneously. For example, companies already certified to ISO 13485 may assume they’re ready for QMSR, but gaps in FDA-specific requirements still exist. Our FDA Consultants help bridge that divide.
Also, the shift encourages early integration of global compliance objectives, reducing duplicate effort and documentation fatigue. However, even globally experienced teams must verify that local adaptations, such as complaint handling procedures and UDI systems, meet FDA expectations under the new QMSR. Ultimately, this regulatory evolution will reward firms that invest early in strategic quality planning and training.
About QMSR: Medical Device Manufacturers Around the World Who Do Business with the U.S. Should Know: The New QMSR and Its Global Impact
Medical device manufacturers worldwide who market or intend to market their products in the U.S. must now comply with QMSR. Again, although this may sound similar to ISO 13485, key differences remain, especially in enforcement and documentation expectations. FDA Consulting plays a vital role in helping international firms adapt to this shift. Even ISO-certified companies may not meet U.S.-specific requirements, such as Unique Device Identification (UDI), complaint handling, and Medical Device Reporting (MDR).
Without careful adjustment, international manufacturers risk receiving Form 483 observations or Warning Letters, even with ISO certificates in hand. Understanding these regulatory layers is essential for continued access to the U.S. market.
Inconsistency of ISO from one country to another
An ISO certification may give a false sense of readiness. A company that succeeds in EU audits may still fail an FDA inspection if it lacks documentation that meets federal expectations. FDA Consulting helps bridge this critical compliance gap. Our FDA Consultants can identify misaligned procedures, train staff on inspection behavior, and guide remediation of U.S.-specific requirements.
Also, global manufacturers often assume their procedures for CAPA, complaint handling, and document control are sufficient. However, FDA inspectors look for precise traceability, decision-making records, and ongoing process improvements. Additionally, non-U.S. facilities must be prepared for unannounced FDA inspections. This is especially true for firms shipping directly into the United States or working with U.S.-based distributors.
Supplier Controls and Importer Relationships
The QMSR introduces enhanced expectations around purchasing controls, supplier qualification, and verification. U.S.-based importers often rely on overseas manufacturers to uphold quality, but the FDA holds both parties accountable for product safety.
Furthermore, U.S. importers may request additional documentation, such as risk management plans, device history records, or inspection-ready SOPs. This is not just regulatory, it’s business-critical. Also, manufacturers outside the U.S. must maintain Design History Files (DHFs) and Device Master Records (DMRs) in formats that align with FDA language and structure. These files are often different from what ISO auditors would expect. Moreover, complaint handling across borders must be streamlined. Time zone differences, language barriers, and miscommunication can delay reporting, increasing regulatory risk.
MDSAP Participation Is Not Enough
Some global manufacturers participate in the Medical Device Single Audit Program (MDSAP), believing it will simplify U.S. compliance. While MDSAP helps, it does not guarantee full QMSR conformity or exemption from FDA inspections. FDA Consulting is often necessary to align MDSAP documentation with the FDA’s expectations under QMSR. Consultants review gaps in audit evidence, clarify misunderstood requirements, and prepare teams for FDA-specific inquiries.
Also, QMSR requires formal management reviews, internal audits, and continuous improvement efforts that go beyond basic ISO checklists. Additionally, global firms must ensure that labeling, tracking, and recordkeeping meet both local and FDA requirements. Harmonization is the goal, but compliance is measured on a country-by-country basis. For long-term success in the U.S. market, understanding QMSR in the context of the FDA, not just ISO, is essential.
Comprehensive FDA Consulting Services, Expert Guidance for Navigating the Complexities of FDA Compliance.
Achieving FDA compliance is not only critical but also a highly regulated process that demands precision. Every step, from product manufacturing to submission strategy, must comply with the Federal Food, Drug, and Cosmetic Act (FD&C Act). Without expert insight, even minor mistakes can lead to noncompliance. For example, simple errors in CAPA can result in significant costs to your company, manufacturing operations, and personnel.
FDA Consulting plays a pivotal role in helping companies understand and comply with these complex regulatory requirements. Consultants guide organizations through various regulatory pathways, ensuring proper documentation, validation, and communication with the FDA. Although many companies have internal regulatory and quality teams, they often lack specialized expertise across all categories. For example, software as a medical device (SaMD) or combination products require distinct regulatory strategies. Furthermore, unintentional omissions or misuse of regulatory terms in submissions, such as 510(k), PMA, or IND, can further complicate matters. Through structured support, FDA consultants can significantly reduce your internal burden and increase the likelihood of successful submissions.
Tailored Solutions for Every Product Type
Each product requires a distinct regulatory approach, whether it’s a medical device or a pharmaceutical. After identifying the product category, consultants assess classification codes, predicate devices (if applicable), and relevant guidance documents.
Consequently, companies gain clear direction on labeling, clinical testing, and premarket pathways. FDA Consulting ensures these strategies are not only compliant but also practical for your business pursuits. Sometimes, businesses enter the compliance process too late or with assumptions based on general information. Therefore, early intervention by qualified consultants can prevent missteps and reduce costly rework. In addition to premarket filings, post-510(k) and post-market compliance are equally important. Adverse event reporting, recalls, CAPA, responses to 483s, and responses to Untitled or Warning Letters, along with QMS audits, must be maintained to meet regulatory expectations.
Quality Systems and Documentation Expertise
Establishing and maintaining a compliant Quality Management System Regulation (QMSR) is one of the most challenging aspects of FDA compliance. This includes design controls, process validation, environmental monitoring, and training protocols. Additionally, many organizations require support in implementing software tools such as eQMS, document control systems, and training platforms. A consultant can recommend systems that align with the FDA’s expectations while remaining efficient for teams.
However, the role of consultants does not end with installation. Many FDA consultants provide training, CAPA remediation, and gap assessments to ensure ongoing compliance.
Strategic Partner for Global Success
Even international companies seeking access to the U.S. market must comply with FDA regulations. Whether your product is CE marked, ISO certified, or approved in another country, FDA submission is required so that your products are not adulterated or misbranded. In this context, FDA Consulting assists non-U.S. companies in localizing their documentation, submitting accurate premarket files, and preparing for facility inspections. No matter your company’s size or industry, having a reliable partner can be the difference between approval and delay.
Global CAPA Integration Across Sites
Multinational companies face unique challenges in aligning CAPA practices across global facilities. Regional expectations, language differences, and cultural norms can create inconsistencies in how issues are identified and addressed. FDA Consulting offers cross-border harmonization, ensuring that CAPA data is integrated into centralized tracking systems that comply with both U.S. and international requirements. Also, electronic systems often lack standardization in closure criteria, root cause selection, or effectiveness checks. This results in regulatory inconsistencies and missed opportunities for systemic improvement.
Moreover, global teams benefit from CAPA training tailored to their functional roles. Quality, manufacturing, engineering, and supply chain each contribute differently and must understand their responsibilities in the process. Furthermore, the FDA frequently inspects overseas facilities that supply the U.S. market. An inconsistent CAPA system can raise red flags, even if the product may be compliant with other countries.
Continuous Improvement Starts with CAPA
CAPA is not only about fixing problems. It is a system for learning and preventing future failures. Data from internal audits, complaints, deviations, and customer feedback must feed into CAPA as part of a closed-loop quality system. Also, CAPA metrics must be actionable. It’s not enough to count open vs. closed cases; companies must track recurrence, delay trends, and overdue actions. Additionally, a mature CAPA program reflects a culture of ownership. Employees are more likely to report issues when they trust the system will act fairly and effectively. Therefore, sustained CAPA maturity is not a project. It’s an ongoing commitment to product quality and regulatory compliance.
FDA Consulting and Mock FDA Inspection under 21 CFR 820 and 21 CFR 210, 211
Medical device and pharmaceutical manufacturers operate under intense regulatory oversight. The FDA conducts routine and for-cause inspections to ensure compliance with 21 CFR Part 820 (Quality System Regulation) and 21 CFR Part 211 (Current Good Manufacturing Practice).
A mock FDA inspection simulates this process in a structured and high-fidelity way. Unlike internal audits, these simulations replicate actual FDA methods, including investigator behavior, inspectional approach, and document requests. Our mock inspection plays a powerful role when preparing for these inspections. Consultants familiar with QMSR and CGMP walk your team through what to expect, step by step. Facilities often assume they’re inspection-ready until documentation is reviewed under FDA standards. Small lapses, such as training records, equipment calibration, CAPA traceability, or validation, can result in major observations. Even well-resourced firms need mock inspections to confirm alignment with updated guidance, FDA priorities, and recent enforcement trends.
Cross-Functional Readiness Is Key
Compliance under 21 CFR 820, 210, and 211 isn’t just a quality department responsibility. Operations, engineering, regulatory affairs, and production must all be prepared for cross-functional interviews and walkthroughs. Mock inspections should include a detailed opening meeting, documentation review, and facility tour. Consultants identify gaps in procedures, execution, and communication during these simulated inspections.
Therefore, mock FDA inspections help companies reduce the anxiety and uncertainty associated with real visits. Teams that rehearse together react more confidently and accurately when under actual scrutiny. FDA Consulting ensures this training is realistic and pressure-tested. Investigators will test how complaints are documented, how change controls are handled, and how production deviations are recorded. Additionally, our FDA consultants frequently issue mock 483s or summary reports that closely follow FDA formatting. These help leadership prioritize risk-based remediation before a real inspection takes place.
What Investigators Look For
Although both device and drug manufacturers must comply with FDA expectations, there are notable differences in what inspectors emphasize under each regulation. 21 CFR 820 focuses on design controls, complaint handling, and production validation. In contrast, 21 CFR 211 places greater emphasis on batch records, laboratory data integrity, and material control. Thus, mock inspections must be tailored to your product category. FDA Consulting is most effective when delivered by professionals familiar with both sectors, or by separate experts where needed.
Additionally, inspectors look for consistency in processes and records. A gap in QMSR can be a red flag. For combination products, both 820 and 211 requirements may apply simultaneously. Furthermore, mock inspections help identify whether your SOPs match actual practice. Investigators often test this alignment by comparing employee responses to written procedures.
The Value of an Investigator’s Perspective
Mock FDA inspections led by our former FDA officials or experienced regulatory consultants offer rare and valuable insight. Our professionals know how real inspections unfold because we’ve conducted them. FDA Consulting, when led by such experts, results in deeper preparation and stronger organizational confidence. For example, a former investigator may detect subtle gaps in batch release documentation or overlooked validation summaries that would otherwise trigger citations. Our experience helps shape response strategies before issues escalate.
Moreover, a strong mock inspection program supports internal audit programs, inspection readiness plans, and management review processes. It encourages a continuous compliance culture. Also, executives gain a more realistic view of their regulatory posture. Instead of relying on theoretical checklists, they see real outcomes under simulated FDA pressure.
We Are All Your Regulatory Affairs Submissions Need. Strategic Planning from Pre-Submission to Approval
Regulatory affairs is more than paperwork; it’s the gateway to market access. Whether you’re preparing a 510(k), PMA, IND, NDA, ANDA, or combination product application, the process demands accuracy, strategy, and deep knowledge of current expectations. Regulatory submission success requires much more than filling out forms. Authorities expect thorough documentation of safety, efficacy, manufacturing controls, and clinical evidence. A single gap can delay or derail the approval process.
FDA Consulting brings specialized insight into these processes. We identify missing data early, manage timelines, and ensure that submission formatting, cross-referencing, and eCopy formatting meet exact standards. Additionally, the pre-submission phase (Pre-Sub, Type C meetings, etc.) is critical. Companies that communicate clearly with regulators early tend to succeed faster and with fewer questions. Additionally, labeling, promotional materials, and risk-benefit analyses must align. These sections are often underestimated, and it is often where submissions falter.
Regulatory Strategy Is Not One-Size-Fits-All
Each product demands a tailored regulatory pathway. Device, drug, and biologic submissions follow different regulatory structures, and combination products often blur these lines. Therefore, planning must start early. FDA Consulting helps sponsors define the optimal pathway by reviewing precedents, classification databases, and FDA guidance documents relevant to their product type. Additionally, a crucial aspect of submission planning is understanding the FDA’s expectations in your therapeutic area. What worked last year may be outdated today, especially as the agency is led by new leadership.
Furthermore, international firms submitting to CDER, CBER, or CDRH must prepare documentation in U.S. regulatory formats. These are not identical to EMA or PMDA requirements.
Submission Readiness
Timelines are tighter than ever. For example, a 510(k) has a 90-day FDA review clock, but the agency can place it on hold if essential content is unclear. In addition, FDA consultants conduct mock reviews of submissions before filing, applying the same lens that FDA reviewers use. This identifies gaps and helps prioritize final QA reviews. Furthermore, manufacturers must align internal departments, quality, regulatory, R&D, and marketing, to produce consistent messaging across the submission.
Even meeting request packages must demonstrate a clear purpose, scientific rationale, and readiness for FDA feedback.
Long-Term Support Beyond Initial Approval
Once a product is approved, the regulatory work doesn’t stop. Post-market submissions, such as supplements, annual reports, and labeling updates, are required throughout a product’s lifecycle.
FDA Consulting provides continuity by supporting sponsors with change control reporting, risk-based design modifications, and lifecycle regulatory strategy. For instance, consultants assist in determining whether a design change requires a new 510(k) or a letter to file. These decisions impact both compliance and commercialization. Moreover, international manufacturers may need to harmonize U.S. updates with their global regulatory strategy, requiring expert coordination. Thus, regulatory success is not a one-time event. It’s a continuous commitment, and choosing the right partner makes all the difference.
We Can Help with CGMP for Pharmaceutical Manufacturers Around the World
Current Good Manufacturing Practice (CGMP) is the foundation of pharmaceutical quality systems. It ensures that drugs are consistently produced and controlled according to quality standards. The U.S. FDA enforces CGMP under 21 CFR Parts 210 and 211, which apply to both domestic and foreign manufacturers shipping to the United States.
Pharmaceutical companies outside the U.S. must comply with these standards if they want to access the U.S. market. That includes facilities in Europe, Asia, Latin America, and beyond.
FDA Consulting is essential in helping global manufacturers interpret the complex and evolving requirements of CGMP compliance. While many companies hold certifications from local authorities, the FDA inspection model places unique demands on documentation, validation, and personnel training. Also, misunderstandings about data integrity, cleaning validation, or laboratory controls can lead to severe enforcement actions. These issues often arise not from bad practices, but from gaps in understanding how FDA investigators interpret evidence.
What to Expect in an FDA Inspection
FDA inspections are typically unannounced, risk-based, and highly focused on critical systems like production, laboratory operations, and quality control. For foreign sites, inspections may involve coordination with international authorities or third-party translators. Therefore, it’s vital to prepare your team in advance. FDA Consulting brings simulation-based training, audit readiness assessments, and procedural review to prepare facilities in a realistic and efficient manner.
Unlike routine audits, FDA inspections emphasize “inspectional observations,” where even a single deficiency in documentation, sterility assurance, or out-of-spec investigation may result in a Form 483. Additionally, the FDA evaluates whether the company’s culture supports quality. That includes how deviations are reported, whether root causes are identified, and how CAPA programs are enforced. Also, inspectors expect real-time access to data, manual logs, electronic records, and raw test results, which must all be complete and accessible at the time of inspection.
Common Pitfalls for Global Manufacturers
One of the most common issues faced by international firms is misalignment between local GMP systems and FDA expectations. Even when drug products meet safety and efficacy standards, the underlying documentation may not pass U.S. scrutiny. FDA Consulting identifies these gaps early, especially in areas like change control, cleaning validation, analytical methods, and batch record completeness.
Furthermore, some facilities underestimate the importance of English-language documentation and English-speaking staff during inspections. Communication errors or delays in document retrieval can be interpreted as compliance risks. In addition, global firms often rely on external laboratories, third-party manufacturers, or brokers, each of which requires qualification and oversight. The FDA holds primary manufacturers responsible for the activities of these partners.
Moreover, issues like equipment calibration, environmental monitoring, and SOP adherence become critical when FDA inspectors evaluate your system holistically.
Building a Stronger Global Compliance Strategy
With pharmaceutical supply chains becoming increasingly globalized, aligning CGMP practices across all sites is a strategic advantage. A well-integrated system reduces audit burden and improves consistency in quality. FDA Consulting empowers your quality team by offering mock inspections, remediation planning, and procedural upgrades that align with U.S. regulations. For example, consultants may help revise batch manufacturing records, train QC personnel in FDA expectations, or install CAPA tracking systems with audit-ready workflows.
Additionally, many foreign manufacturers benefit from readiness assessments conducted before pre-approval inspections (PAI). This minimizes surprises and strengthens sponsor confidence in their global partners. Also, companies exporting to the U.S. must understand that FDA enforcement is escalating in areas like data falsification, cross-contamination, and failure to investigate discrepancies. Thus, preparation is not optional. It’s a business-critical obligation for global pharmaceutical companies aiming to succeed in the U.S. market.
FDA Inspections Require Strategy, Not Just Documentation
We assist with your upcoming FDA inspection as an Advisor. When the FDA announces or initiates an inspection, how you prepare makes all the difference. Your procedures, records, and personnel must be ready, but so must your mindset, coordination, and risk management.
FDA inspections are often unannounced and follow a highly structured format based on Compliance Program Guidance Manuals (CPGMs). Being technically compliant is important, but being inspection-ready is essential. FDA Consulting offers pre-inspection advisory support for pharmaceutical, medical device, and biologics firms. We guide your team in real time to anticipate questions, manage interviews, and maintain a professional inspection atmosphere. Also, we conduct readiness walkthroughs, document reviews, and mock interviews simulating the FDA’s approach under 21 CFR Parts 211, 820, and others.
Therefore, companies don’t just need compliance; they need an inspection execution strategy. Our advisory approach reduces stress, aligns leadership, and ensures continuity. Furthermore, we remain available during the actual inspection for on-call clarification, coaching, and damage control if surprises arise.
What We Do as Your FDA Inspection Advisor
An inspection advisor acts as your behind-the-scenes expert. While we don’t speak directly to investigators, we help your internal teams stay coordinated, accurate, and confident throughout the process. FDA Consulting provides playbooks for documentation retrieval, SME (Subject Matter Expert) identification, and daily inspection briefings.
Also, we help you manage the inspection scope. Inspectors may deviate from the original purpose if they uncover issues in unrelated areas. We guide you in staying on topic and managing redirection. Additionally, we assist with inspection room logistics, response time tracking, and inspection etiquette, all of which influence how the agency perceives your quality culture. Moreover, we review records before submission to catch inconsistencies or gaps that may raise red flags. Furthermore, if a 483 is issued, we help draft a strategic and timely response that demonstrates both accountability and effective CAPA planning.
Mock Inspections and Real-Time Coaching
Mock inspections are one of the best tools to prepare for real inspections. These simulations identify weaknesses not only in documents and systems, but also in personnel behavior and readiness. FDA Consulting performs targeted mock inspections using FDA-style techniques, observation tracking, and investigator-style questioning. Also, we provide immediate coaching to SMEs on how to answer questions, handle follow-ups, and reference documentation accurately without speculation.
After the Inspection: Response and Recovery
Post-inspection actions are just as important as the inspection itself. How you respond to a Form 483, verbal observation, or Establishment Inspection Report (EIR) reflects your quality maturity. FDA Consulting assists clients in prioritizing inspection findings, drafting 15-business-day responses, and managing CAPA execution timelines. Additionally, we provide support with post-inspection internal reviews, leadership debriefs, and communication strategies to ensure transparency and ongoing improvement.
Also, for high-risk findings, we support escalation planning, board-level reporting, and legal risk assessments. Moreover, we assist with re-inspections or follow-up engagements related to prior deficiencies. Therefore, FDA inspection advisory support extends beyond the inspection window. It encompasses the entire lifecycle, from preparation to defense and recovery.
Why Gap Assessments Are a Strategic Necessity
A gap assessment is a systematic comparison between your current practices and regulatory expectations. Whether preparing for FDA inspection, ISO certification, or a product submission, a well-executed gap analysis reveals where risks exist and what needs to change. Gap assessments are not just compliance tools. They are business intelligence mechanisms for improving quality, reducing the cost of poor quality, and managing regulatory exposure.
FDA Consulting specializes in comprehensive gap assessments across regulatory frameworks: 21 CFR Part 820, Part 211, ISO 13485, EU MDR, and more. Also, we tailor each assessment to your facility, product line, and compliance history. One-size-fits-all checklists often miss contextual risks or overemphasize irrelevant areas. Therefore, our approach combines documentation review, personnel interviews, facility walkthroughs, and risk scoring to provide an accurate, prioritized action plan. Furthermore, our final reports map findings directly to applicable regulations, making it easier for your quality and compliance teams to act.
When and Where to Use Gap Assessments
Gap assessments are critical at multiple points in the product and compliance lifecycle. Companies preparing for FDA inspections, ISO audits, remediation projects, or product submissions benefit most when they assess early. Additionally, they are vital when implementing new QMSR systems, acquiring facilities, or expanding into new markets. FDA Consulting helps determine the scope and depth of your gap assessment, whether focused on CAPA, validation, design control, data integrity, or overall QMS performance. Also, during mergers and acquisitions, we provide objective third-party assessments of compliance posture to support due diligence.
Moreover, startups entering the U.S. market need pre-submission gap analysis to align technical documentation and quality processes with FDA expectations. Furthermore, for companies under a consent decree or operating under Warning Letters, gap analysis becomes the cornerstone of remediation strategy. Thus, no matter the phase, an effective gap assessment prevents reactive firefighting later.
What Makes a Good Gap Assessment?
A good gap assessment doesn’t just find issues. It explains their impact, priority, and path to resolution. It must distinguish between observations that are low-risk and those that could halt production or delay approval. Therefore, context and experience are everything. FDA Consulting brings former investigators, auditors, and industry veterans to the table. Also, a strong gap report provides traceability. Each observation links directly to regulations or guidance (e.g., 21 CFR 820.100, ISO 13485:2016 Clause 8.5.2, etc.). Additionally, the assessment must evaluate system maturity: Are procedures followed? Are they effective? Are people trained in them?
Moreover, your team should be involved during the assessment process, not just after it ends. That way, the findings become learning opportunities, not just audit surprises. Also, a post-assessment workshop helps translate gaps into CAPA actions, ownership, and timelines with leadership support.
Closing Gaps with Confidence
Finding gaps is only the first step. Closing them correctly, efficiently, and permanently is the goal. FDA Consulting assists with CAPA plans, remediation project management, SOP updates, and training tailored to address your unique findings. For example, if the assessment revealed repeated deviations tied to cleaning validation, we can redesign protocols, retrain staff, and guide requalification studies. Also, we ensure documentation of closure is audit-ready, with objective evidence, effectiveness checks, and quality system updates.
Furthermore, closing gaps may involve IT system upgrades, restructured quality teams, or realignment of QMSR responsibilities. Additionally, we help benchmark progress through periodic mini-assessments that keep remediation projects on track. Thus, gap assessments are not checklists. They are roadmaps to sustained quality and regulatory confidence.
Quality Training That Matches Real-World Expectations
We Train Your Employees on Updated Quality System Regulations and Requirements, Including CGMP and QMSR. Training is not just a checklist item. It is the foundation of regulatory compliance and product quality. The FDA and international regulators expect that every employee involved in manufacturing, testing, or reviewing regulated products is trained on the current regulations, applicable SOPs, and job-specific tasks. With the release of the FDA’s new Quality Management System Regulation (QMSR) and the ongoing enforcement of current Good Manufacturing Practice (CGMP) under 21 CFR Parts 210, 211, and 820, outdated training is no longer acceptable.
FDA Consulting provides targeted training programs designed for manufacturing, QA, QC, regulatory affairs, and executive leadership. Also, our training modules go beyond PowerPoint slides. They incorporate real case studies, mock audit exercises, and interactive quizzes that simulate FDA inspection scenarios. Therefore, employees don’t just learn, they practice applying quality and compliance thinking to daily activities. Furthermore, we customize content for your product type, role functions, and risk profile.
What the FDA Expects from Your Training Program
The FDA does not require a specific training format, but it does expect documentation of effectiveness. That means records showing the content, attendees, trainer credentials, and most importantly, how well employees retained and applied the information.
FDA Consulting helps you build a compliant and effective training matrix across departments and locations. Also, we design role-specific curricula for personnel who need training in CGMP, QMSR, data integrity, cleaning validation, complaint handling, or design control. Additionally, we help clients establish SOPs for training governance, retraining after deviations, and requalification for critical roles. Moreover, during FDA inspections, training records are often the first documents requested. Investigators may even interview operators to check their knowledge against SOPs. Thus, your training program must prepare your team not only for compliance but also for real-time inspection response.
Adapting to Regulatory Change with Confidence
With QMSR replacing the previous 21 CFR 820 framework, companies must now align training content with ISO 13485:2016 principles. But CGMP expectations for drug and biologic manufacturing remain distinct and robust. FDA Consulting bridges this gap by tailoring sessions to highlight both the harmonization points and the regulatory differences. Also, our instructors include former FDA officials and industry veterans who understand what inspectors look for and what they consider red flags. Additionally, companies undergoing remediation after 483s or Warning Letters often require targeted retraining as part of their CAPA commitments. We design programs that fulfill these obligations and demonstrate a culture of continuous improvement. Therefore, staying up to date with regulatory changes isn’t optional—it’s part of operational survival.
Building a Culture of Quality Through Education
Training should not feel like a chore. When done well, it motivates employees to own their role in quality and compliance. FDA Consulting provides train-the-trainer programs to support internal scalability and long-term knowledge retention. Also, we evaluate training effectiveness using knowledge checks, behavioral observations, and feedback forms. These metrics help identify gaps before they become audit findings. Additionally, refresher training is essential for maintaining readiness. We offer annual CGMP and QMSR updates aligned with the latest FDA and ISO guidance. Moreover, new employee onboarding modules ensure your workforce starts strong and understands your expectations from day one. Thus, training is not just education; it’s a strategic tool for compliance, efficiency, and team empowerment.
FDA Warning Letters Are Not Just Formalities
See our expertise when responding to the FDA Warning Letter or Inspectional Observations Form-483, unqualified answers can escalate further. Receiving an FDA Form 483 or Warning Letter is a serious regulatory milestone. These documents represent unresolved compliance concerns observed during an inspection, and how you respond can determine whether the situation escalates.
A poorly written or late response may lead to product seizures, import alerts, or even a consent decree. More importantly, it damages your company’s reputation with regulators and stakeholders.
FDA Consulting provides immediate assistance in crafting responses that are complete, timely, and tailored to the specific language and intent of the observation. Also, we help you interpret what the FDA is truly saying. Observations are often written tersely and without context—our experts translate them into actionable priorities. Therefore, our goal is not just to answer the letter, but to rebuild confidence in your quality system and demonstrate regulatory maturity. Furthermore, our support includes CAPA development, systemic remediation planning, and strategy briefings for executive leadership.
Crafting a Response the FDA Will Respect
A successful response to a 483 or Warning Letter has three key elements: a clear understanding of the issue, a root cause analysis, and a detailed plan to correct and prevent recurrence. FDA Consulting specializes in developing responses that reflect sincerity, capability, and structure. We help you avoid vague statements, unjustified delays, or excuses that weaken your credibility. Also, we guide teams in defining measurable corrective actions with owners, target dates, and effectiveness checks.
Moreover, we help you anticipate how the FDA might evaluate your plan. Will they consider it sufficient? Will they expect a follow-up inspection? We prepare you for both possibilities. Thus, our approach is not reactive. It’s strategic and forward-looking.
Avoid Escalation by Acting Decisively
Unqualified or casual responses are a common reason that Warning Letters escalate to enforcement. Statements like “we’ll correct them” without evidence or timelines signal a lack of control. FDA Consulting ensures that your response reflects leadership oversight, cross-functional involvement, and permanent system changes. Also, we help document progress while implementation is ongoing. Interim controls, updated SOPs, and risk mitigation plans show you’re not waiting for change; you’re executing it. Furthermore, we support communication with the FDA post-submission, including updates, clarifications, or responses to follow-up questions.
Additionally, companies under scrutiny benefit from having our team prepare for re-inspection, mock walkthroughs, and document readiness checks. Therefore, strong response management is both regulatory compliance and corporate risk reduction.
Building a Better Quality System From the Ashes
While no company wants a Warning Letter, the remediation process is an opportunity to redesign a stronger, more resilient quality system. FDA Consulting helps clients not only close the findings but also evaluate how those findings reflect deeper system gaps.
Sterilization Validation Is Not Optional. Consult with Us for Sterilization Validation Expertise
Sterilization validation is a mandatory requirement for any medical device, pharmaceutical, or combination product labeled as sterile. The FDA and global regulatory authorities require documented evidence that the sterilization process consistently achieves the defined sterility assurance level (SAL), typically 10⁻⁶. Incorrect or incomplete validation can lead to patient harm, product recalls, or enforcement actions. FDA Consulting offers specialized guidance across multiple sterilization modalities, including ethylene oxide (EtO), steam, dry heat, radiation, and aseptic processing validations. In addition, each method requires a distinct approach to cycle development, load configuration, and placement of biological indicators (BI). Templates and generic protocols are not sufficient.
Therefore, your validation program must be tailored to the specific product, packaging system, and process controls involved. Proper dose mapping, equipment qualification, and environmental monitoring are essential for a compliant result. Furthermore, sterilization validation must be integrated into change control, product development, and supplier oversight systems.
Process Control and Documentation Expectations
Sterilization validation is not just about passing a biological indicator test. It is about process repeatability and robust documentation that can stand up to regulatory review. Moreover, validation protocols must include pre-approved acceptance criteria, clear responsibilities, and justifications for cycle parameters and BI placement. FDA Consulting assists in preparing detailed validation master plans (VMPs), executing performance qualification (PQ) runs, and generating comprehensive summary reports.
Also, the FDA often inspects sterilization facilities, both in-house and contract service providers. Each site must demonstrate equipment calibration, control chart monitoring, and validated procedures. Additionally, all critical records, including BI lot certifications, temperature and pressure logs, and alarm reviews, must be available in real-time during inspection. Furthermore, firms must be prepared to defend their sampling plans, hold-time studies, and packaging integrity validation when requested. Thus, sterilization validation must be inspection-ready at all times, regardless of whether it’s a contract site or internal process.
Challenges in Aseptic Processing and Combination Products
Sterilization becomes even more complex in aseptic processing, where components are sterilized separately and assembled in classified environments. The FDA expects companies to validate each step independently and holistically. FDA Consulting assists with process simulation studies (media fills), cleanroom qualification, air quality monitoring, and operator training documentation. Also, combination products involving device-drug or device-biologic components require harmonized validation approaches. For example, gamma sterilization may impact drug stability or device performance, necessitating compatibility testing. Furthermore, aseptic processes must be supported by rigorous environmental monitoring programs, HEPA filter certifications, and validated gowning protocols.
Moreover, the design of facilities and HVAC zoning becomes part of the validation conversation. Regulatory agencies may inspect cleanrooms as part of the overall sterilization process control. Therefore, cross-functional coordination between manufacturing, quality, regulatory, and engineering teams is crucial.
Risk-Based Validation and Lifecycle Monitoring
Sterilization validation is not a one-time task. It requires requalification, annual reviews, and continuous data trending. Risk-based validation ensures that you focus resources where the failure impact is highest. FDA Consulting supports the creation of risk assessments, validation frequency plans, and routine requalification protocols based on process complexity and product criticality. For example, a facility using EtO may require requalification after every major load configuration change or adjustment to a cycle parameter. Also, ongoing monitoring is expected. This includes biological indicator trends, process deviation investigations, and nonconformance tracking linked to the sterilization process.
Additionally, regulatory bodies increasingly expect alignment with international standards such as ISO 11135, ISO 11137, or Annex 1 of EU GMPs. Thus, your sterilization validation strategy must reflect both U.S. and global compliance demands.
Responding Effectively to Adverse Events and Recalls
Medical Device Reporting (MDR) and recall investigations are among the most scrutinized activities in FDA-regulated industries. These processes require speed, accuracy, and deep knowledge of regulatory expectations to protect patients and maintain market access. When an adverse event occurs or a product defect is discovered, your response time and the quality of your documentation can determine the outcome of an inspection or enforcement action.
FDA Consulting assists clients in managing MDRs, Vigilance reports (EU), and recall investigations, ensuring every detail aligns with 21 CFR Parts 803, 806, and 7 Subpart C. Additionally, we assist you in determining whether an event is reportable, provide guidance on documenting the investigation, and instruct you on how to submit it to the FDA’s MDR system.
Investigating with Root Cause and Risk in Mind
Not all MDRs lead to recalls, but all must be thoroughly investigated. The FDA expects documentation of complaint evaluation, root cause analysis, and a defined risk assessment. Also, timing is critical. Most MDRs must be submitted within 5 or 30 calendar days, depending on the event. Missed deadlines or vague justifications trigger warning letters and Form 483s. FDA Consulting supports the development of investigation templates that cover all FDA-required elements, including event description, root cause logic, and corrective actions. Moreover, we help ensure cross-functional involvement in decision-making: quality, engineering, clinical, and regulatory must align on the risk level and disposition.
Additionally, if a recall is necessary, we guide clients through classification, strategy submission, lot traceability, and effectiveness checks. Thus, we help transform investigation data into regulatory-ready responses that protect both patients and your company’s reputation.
Recall Management That Withstands FDA Scrutiny
When a product poses a potential health risk, prompt recall action is essential. However, recalls must be initiated and managed in accordance with strict FDA procedures. FDA Consulting helps companies develop recall strategies, draft notifications, and coordinate communication with distributors, healthcare providers, and patients. Additionally, we assist you in determining the recall scope, affected lot ranges, and correction versus removal status, in accordance with 21 CFR Part 7 guidelines.
Furthermore, the FDA expects firms to demonstrate effectiveness checks for 100% of consignees. Poorly managed recalls can result in escalation to enforcement actions or consent decrees. Additionally, we train your team on how to handle FDA recall audits. Inspectors often request your full investigation file, internal communications, and CAPA links. Moreover, we help you maintain records that are inspection-ready before the agency knocks on your door. Therefore, recall management is not just a regulatory obligation; it’s a brand protection strategy.
Long-Term Improvements from Short-Term Incidents
Every adverse event or recall is a chance to improve. Once the crisis passes, companies must evaluate what failed and how systems can be improved to prevent recurrence. FDA Consulting provides post-recall debriefs, CAPA planning, and management review support to help organizations close the loop effectively. Additionally, we analyze historical complaint trends to identify early warning signals that may have been overlooked.
Furthermore, companies with complex supply chains benefit from supplier investigation protocols, contract language reviews, and audit coordination. Additionally, we support revisions to complaint handling SOPs, MDR decision trees, and recall readiness procedures. Thus, we help clients not only survive investigations but also emerge stronger and more inspection-ready.
We Will Use Our FDA Experience to Help You Any Way We Can. We Are on Your Side! We Work for You.
Experience You Can Count On. Because We’ve Been There
Navigating FDA regulations is difficult unless you’ve lived it from the inside. Our team includes former FDA investigators, compliance officers, and industry professionals who know exactly how the system works. We’ve conducted inspections, issued 483s, and reviewed responses. Now we use that experience to guide and protect your business. FDA Consulting offers advisory services grounded in real-world enforcement experience. We help you understand how the FDA thinks, what their priorities are, and how to respond with clarity and credibility.
Also, our insight into inspection trends, regulatory focus areas, and risk indicators helps you stay ahead of compliance issues before they escalate. Therefore, when you work with us, you’re not guessing what the agency wants. You’re guided by people who once stood on the other side of the table. Furthermore, we adapt our support to your team, product, and risk profile, not based on theory, but based on what works.
FDA Consulting that Works for You, Not the FDA
Our only mission is to help you succeed. That means you can ask us anything, share confidential concerns, and know we’re 100% on your side. We build trust with clients by listening first. We understand your challenges before recommending solutions. Also, we take pride in being responsive, respectful, and practical, not rigid or theoretical. We work as an extension of your team, not as outsiders. Additionally, we stay involved through the entire project—no handoffs, no confusion, no ghosting. The person you meet first is often the same person who stands by you during an inspection or audit. Moreover, we know how important it is to speak your language—technical, operational, and regulatory. Thus, our FDA experience doesn’t make us intimidating. It makes us effective advocates for your business.
Support in High-Stakes Moments
You need steady guidance during moments of pressure: inspections, Warning Letters, recalls, submissions, or consent decree negotiations. FDA Consulting provides calm, structured, and strategic support when the stakes are highest. Also, we prepare inspection response plans, coach teams before FDA site visits, and guide communication during active audits.
Furthermore, we can remain on standby during inspections to answer questions, review documentation, and troubleshoot issues that arise unexpectedly. Additionally, we help you frame your responses to the FDA with the right tone, accountable, precise, and improvement-focused. Moreover, our post-inspection services include CAPA planning, response drafting, risk communication, and mock re-inspections to validate closure. Therefore, our role is not just consulting—it’s protecting your company’s credibility when it matters most.
FDA Knowledge That Builds Long-Term Strength
Our goal is not just to fix the problem today, but to help you prevent problems tomorrow. That’s why we embed our knowledge into your processes, training, and quality culture.
FDA Consulting supports sustainable improvement by providing SOP revisions, internal audit templates, training materials, and quality dashboards. Also, we empower your internal teams with the same knowledge we used as regulators. Furthermore, we help your leadership interpret FDA guidance documents, enforcement trends, and premarket expectations in plain language. Additionally, our collaborative approach helps your team build confidence, so they can lead future inspections and audits independently.
Thus, we bring FDA experience to your side and stay with you until your team can stand on its own.
Contact Us Today. We Travel Around the Globe. Since Our Priority Is Our Current Clients, Become One Today.
Compliance Support That Comes to You, Anywhere
Global compliance doesn’t happen from behind a desk. Whether you’re in California, Germany, Switzerland, or Japan, regulatory expectations are the same, and so is our commitment to helping you meet them. FDA Consulting travels to client sites worldwide to support inspections, conduct gap assessments, lead validation activities, and deliver training programs tailored to your exact regulatory environment. Also, we understand that remote audits and virtual reviews can only go so far. Onsite engagement is necessary to observe operations, coach personnel, and resolve issues in real time. Therefore, our global mobility is not a convenience. It’s a strategic part of how we work.
Why Priority Clients Receive Full Access
Our calendar fills quickly because we limit the number of engagements to maintain quality and responsiveness. Unlike transactional firms, we treat every active client as a priority. FDA Consulting allocates resources in advance, ensuring availability when it matters most before and during inspections, submission deadlines, or remediation timelines. Also, existing clients receive real-time access to our experts via email, phone, or secure portals, without waiting in line.
Additionally, we build ongoing relationships that evolve with your quality system. From your first 510(k) to global expansion, we stay involved, not just until payment clears, but until results are delivered. Moreover, by focusing on current clients, we minimize project delay risk and ensure knowledge retention within your team. Thus, becoming a client means you secure priority access to our time, attention, and global network.
Full-Spectrum Support at Every Stage
Whether you are launching a new product, facing a regulatory challenge, or building a sustainable quality culture, we meet you where you are, literally and strategically. FDA Consulting supports early-stage startups, established manufacturers, and international suppliers with services including PAI readiness, CGMP remediation, QMSR alignment, and MDSAP gap assessments. Also, our advisors assist onsite with document preparation, internal audits, mock inspections, supplier qualification, and board-level briefings. Furthermore, we can support single sites or deploy across networks of facilities to ensure consistency across your global operations. Additionally, we offer customized training for new hires, SMEs, and executive leadership—delivered in your language, time zone, and preferred format. Therefore, when you become a client, you gain access to scalable solutions designed for long-term growth and regulatory success.
Take the First Step Today. It Starts with a Call
Every successful project starts with a simple conversation. We assess your current challenges, discuss your goals, and propose a roadmap tailored to your needs. FDA Consulting schedules discovery calls quickly and discreetly. No pressure. No boilerplate sales pitch. Just honest insights from advisors who know how to help. Also, our global travel capacity means we can be at your site when you need us, not weeks later when it’s too late. Also, early engagement allows us to reserve the resources and advisors best suited to your project type and timeline.
Moreover, regulatory agencies don’t wait, and neither should you. Priority access begins the moment you engage.
Thus, contact us today. Because when it’s your turn to face the FDA, we’ll already be by your side.